Fachartikel vom 06/08/2012
Zukunftssicheres Montagekonzept für Luxus-Rasierer
Konsequent flexibel
Hightech-Rasierer von Philips sind weltweit gefragte Premiumprodukte. Sie werden nicht in Fernost montiert, sondern im niederländischen Drachten. Dabei bringen rund 120 Roboter, eingebettet in ein wegweisendes Montagekonzept, die Faktoren Qualität, Wirtschaftlichkeit und Flexibilität in Einklang.
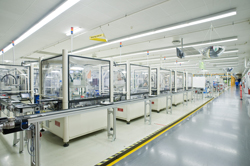 |
Die wegweisenden Automatisierungslösungen machen das Philips Werk in Drachten zu einem der weltweit innovativsten Produktionsstandorte für Elektrorasierer. (Bild: Adept Technology) |
Die Produktion von Elektrorasierern steht unter immensem Kostendruck. Das Angebot an Geräten im Handel ist enorm. Neben Qualität und Design beeinflusst auch der Preis die Kaufentscheidung. Um unter diesen Bedingungen wettbewerbsfähig anbieten zu können, setzt Philips auf zwei Produktionsstandorte. Einer davon befindet sich in China, der andere in Drachten. Während in China heute rund 20 Millionen Apparate mit zwei Scherköpfen jährlich entstehen, produzieren die rund 1.500 Beschäftigten des Werkes Drachten etwa acht Millionen edle Luxusrasierer mit drei Scherköpfen im Jahr. In Drachten ist auch das Forschungs- und Entwicklungszentrum von Philips angesiedelt. Hier werden alle neuen Philips Rasierer, vom einfachen Standardmodell bis zum Hightech-Apparat entwickelt.
Die Montage dieser Hightech-Geräte stellt höchste Anforderungen an die Qualität: Während in China bei der Montage der Standardrasierer Handarbeit dominiert, ist im Werk Drachten Automation angesagt. Prozesssichere Montageschritte mit integrierter Qualitätssicherung garantieren Endprodukte auf allerhöchstem Niveau. Wie man die nötigen Anlagen für anspruchsvolle Montageaufgaben baut, ist für die Bremer Werk für Montagesysteme GmbH kein Geheimnis. Die Spezialisten verfügen über das entsprechende Know-how, doch im Falle Philips war weit mehr gefragt als solide Lösungen von der Stange.
„Die eigentliche Herausforderung bei der Philips Lösung lag in der Bewältigung der enormen Variantenvielfalt der High-End-Rasierer. Aktuell gipfeln rund 60 verschiedene Produktfamilien in etwa 600 einzelnen Produkten. Dabei ändert sich das Produktspektrum beinahe täglich“, so Matthias Schaller, Leiter Robotik der Bremer Werk für Montagesysteme GmbH. Und: Philips definierte eine Anforderung an die Montagelösung, die weit mehr als nur Weitblick von den Konstrukteuren der Anlage forderte: So verlangten die Niederländer eine bis dato nie gekannte Zukunftssicherheit der Anlage. Dazu Sietze Bremer, Senior Sourcing Specialists Industrial bei Philips: „Wir wollten ein Montagekonzept der Zukunft realisieren und uns im Hinblick auf die Gesamtinvestition sicher sein, dass wir auf den Anlagen auch noch in zehn Jahren Rasierapparate wirtschaftlich produzieren können, ohne zu wissen, wie die Rasierer der Zukunft überhaupt aussehen werden.“ Flexibilität war also gefordert und zwar durchgängig.
Die Lösung: flexible Komponenten aus einer Hand
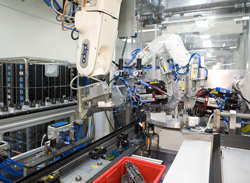 |
Adept Viper 6-Achs-Roboter bei der Montage des Rasierapparates (Bild: Adept Technology) |
Wie baut man Anlagen für die Montage von Produkten, von denen heute niemand sagen kann, wie sie in Zukunft aussehen und funktionieren werden? Eine Aufgabe, die den Ehrgeiz und die Kreativität der Bremer auf eine harte Probe stellte. Die Lösung hieß Adept. Warum, erklärt Automationsstratege Schaller: „Nach ersten Analysen kristallisierte sich ein Anlagenkonzept heraus, das nur auf hochflexiblen Automatisierungskomponenten aus einer Hand funktionieren konnte. Bei der Vielzahl an Montagestationen und -linien hätte ein Komponentenmix von unterschiedlichen Herstellern zu einer nicht mehr kontrollierbaren Komplexität geführt. Was wir also brauchten, waren Sechsachser, Scaras, Visionsysteme, Zuführeinrichtungen und Steuerungen aus einer Hand. Wir setzten hierbei auf Adept, deren hochleistungsfähige Komponenten allen Anforderungen gerecht werden und uns in der Vergangenheit die Leistungsfähigkeit in ähnlichen Projekten nachgewiesen haben.“
Aber der Reihe nach: Grundsätzlich sind es drei Faktoren, die ein Höchstmaß an Flexibilität garantieren. Das ist zum einen der modulare Aufbau der Rasierapparate, die im Wesentlichen aus drei Komponenten bestehen. Diese Komponenten können unabhängig voneinander auf unterschiedlichen Linien gefertigt werden.
Faktor zwei ist die Konzeption der kompletten Anlage, der ebenfalls der Modulgedanke zugrundeliegt. Derzeit erfolgt die Montage der 3-Kopf-Rasierer in Drachten auf insgesamt neun Längstransfer-Montagelinien, bestehend aus jeweils fünf bis acht Zellen. Dabei ist jede Zelle vollkommen autonom aufgebaut und kann nach dem plug & play-Prinzip jederzeit an- oder abgekoppelt werden. Aktuell wird die komplette Anlage um vier neue Linien erweitert. Das Konzept der kleineren, voneinander unabhängigen Linien mit autarken Zellen ist nicht nur Flexibilitätsbooster, sondern steht auch für maximale Verfügbarkeit. Denn: Hakt es an einer Stelle, steht nicht gleich die komplette Anlage, sondern eben nur eine der Linien.
Über 120 Roboter und 40 Anyfeeder
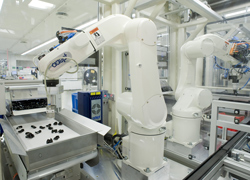 |
Adept Viper Roboter übernehmen eine Vielzahl anspruchsvoller Pick&Place-Aufgaben (Bild: Adept Technology) |
Nach Integration der neuen Linien werden es über 120 Adept Roboter und 40 Adept Anyfeeder sein, die für eine reibungslose Montage der Rasierapparate sorgen. Und eben diese Adept-Komponenten erweisen sich als dritter, entscheidender Flexibilitätsfaktor. „Auch bei der Erweiterung der Anlage setzen wir voll und ganz auf Adept. Die Sechsachser Viper s650 und s850 sowie die Scaras der Cobra-Baureihen s350, s600 und s800 sind überwiegend mit dem Bildverarbeitungssystem Adept Sight ausgestattet und haben sich in den bereits bestehenden Linien bestens bewährt. Die Roboter überzeugen mit Präzision, Geschwindigkeit sowie hoher Verfügbarkeit und erfüllen auch die Aufgabenstellungen mit höchsten Genauigkeitsanforderungen.
Eine Schlüsselrolle innerhalb der Zellen kommt dem Anyfeeder zu, ohne dessen anerkannter Flexibilität das Anlagenkonzept in dieser Form wohl nicht zu realisieren gewesen wäre“, so der erfahrene Senior Manager Sietze Bremer. Tatsächlich haben sich die Zuführsysteme Anyfeeder in der Montageautomation überall dort einen Namen gemacht, wo es auf wirtschaftliche Montage mit hohem Individualisierungsgrad ankommt.
Das Bremer Werk für Montagesysteme setzt in den Philips Anlagen auf den Adept Anyfeeder SX 240, der im Zusammenspiel mit den Robotern der Cobra- oder Viper-Serie und der Bildverarbeitung Adept Sight den Begriff Flexibilität bei der Zuführung von Kleinteilen neu definiert. „Flexible Zuführungen sind Schlüsselkomponenten für die intelligente Montageautomation und insbesondere für die Zukunftsfähigkeit der Philips-Anlage. Egal wie die Einzelteile für die Rasierapparate in Zukunft aussehen werden, der hochflexible AnyFeeder führt sie als Schüttgut zu, die sehenden Roboter greifen sie ab und bauen daraus die Geräte. An diesem einfachen Grundprinzip wird sich auch in zehn Jahren nichts ändern“, so Schaller.
Bildverarbeitung ab sofort obligatorisch
Was sich geändert hat, ist die Ausstattung der knapp 50 Roboter für die vier neuen Montagelinien, die sich derzeit im Bau befinden. Ist bereits ein Großteil der Roboter an den bestehenden Linien mit Bildverarbeitungssystemen ausgestattet, werden die neuen Maschinen allesamt über Visionsysteme verfügen. Auch das ein Zugeständnis an die Flexibilität: „Ein Roboter mit integrierter Bildverarbeitung lässt sich perfekt für wechselnde Aufgabenstellungen einsetzen und kann zudem zusätzliche Arbeitsinhalte beispielsweise in der Qualitätssicherung übernehmen“, so Bremer.
Die wegweisenden Automatisierungslösungen garantieren eine wirtschaftliche und effiziente Montage der High-End-Rasierapparate. Das ausgeklügelte Montagekonzept garantiert in Verbindung mit den innovativen Komponenten aus einer Hand eine bis dato nicht erreichte Zukunftsfähigkeit und macht das Philips Werk in Drachten zu einem der weltweit innovativsten Produktionsstandorte für hochwertige Rasierapparate. (il)
Zum Autor:
Rüdiger Winter ist Director Sales Europe bei der Adept Technology GmbH